Top-Quality Rubber Hoses for Industrial Use in the UK
By:Admin
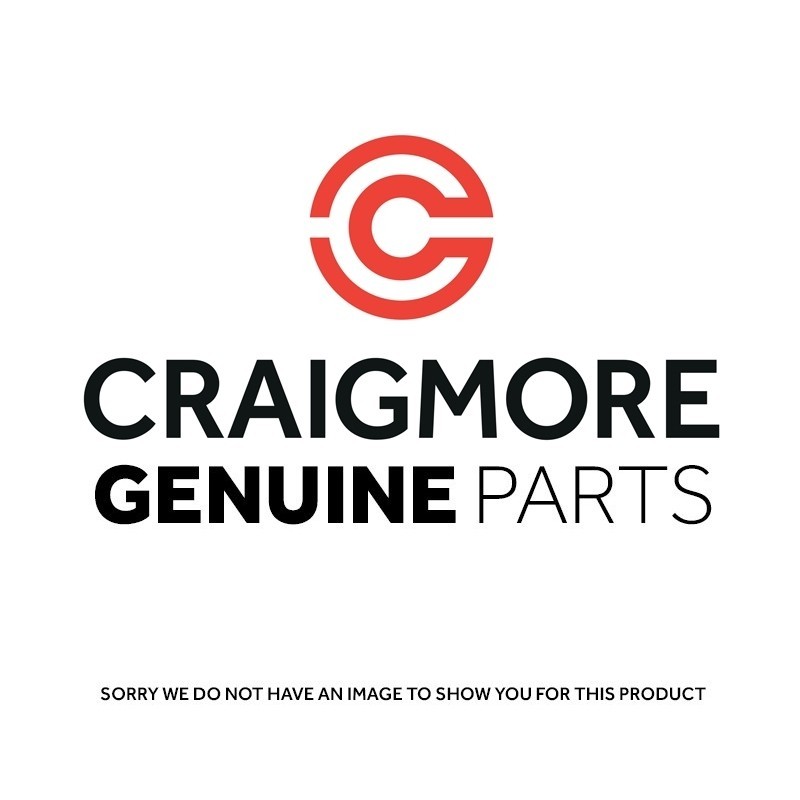
Rubber hoses are undeniably one of the most crucial components of any industrial setting. They are responsible for transporting various fluids, gases, or even solids from one point to another with ease and accuracy. Different industrial settings require various hose types, but for heavy-duty applications, a rubber hose is undoubtedly the go-to option.
A heavy-duty rubber hose is a type of industrial hose designed to withstand demanding working conditions such as high temperatures, high pressure, abrasion, and harsh chemicals. These hoses are typically made of synthetic rubber materials that offer superior durability and resistance to wear and tear.
The Importance of Heavy-Duty Rubber Hoses
Heavy-duty rubber hoses are used in a wide range of applications, including construction, mining, agriculture, marine, and automotive industries. These hoses are designed to handle complex and challenging applications, where typical hoses may fail to perform. Some common benefits of heavy-duty rubber hoses include:
1. Durability: Heavy-duty rubber hoses are designed to withstand harsh conditions and provide extended service life. They have a higher resilience to abrasion, puncture, and cuts, making them ideal for heavy-duty applications.
2. High-temperature resistance: Rubber hoses can handle a wide range of temperatures without experiencing any deformation or damage. This quality makes them ideal for applications requiring high-temperature resistance.
3. Chemical resistance: Heavy-duty rubber hoses are highly resistant to various chemicals that would otherwise damage typical hoses. This makes them suitable for the transportation of various fluids, including acids and alkalis.
4. Application versatility: Heavy-duty rubber hoses can be used in different industrial settings, including hydraulic systems, pneumatic systems, and water delivery systems.
Selecting the Right Heavy Duty Rubber Hose
When choosing a heavy-duty rubber hose, it's essential to consider the specific application requirements. Here are a few factors to consider when selecting a heavy-duty rubber hose:
1. Pressure rating: Make sure the hose can handle the required operating pressure of the application. It's crucial to select a hose with a higher operating pressure than your application requires to avoid any damage or failure.
2. Temperature rating: Consider the temperature range of the application to ensure the hose can withstand these temperatures.
3. Hose diameter: The diameter of the hose determines its flow rate. Select a hose with the appropriate diameter to achieve optimal flow rate and performance in your application.
4. Abrasion resistance: For applications with high abrasion, choose hoses with higher abrasion-resistant covers. This ensures the hose's extended service life in a demanding environment.
Conclusion
A heavy-duty rubber hose is a crucial component in many industrial applications. These hoses offer superior durability, resistance to wear and tear, temperature, and chemical resistance, and versatility. It's essential to choose the right heavy-duty rubber hose that meets specific application requirements to ensure optimal performance, safety, and durability. Whether you need hoses to transport fluids, air, or gas in industrial applications, a durable, heavy-duty rubber hose is the best option to consider.
Company News & Blog
High-quality Trunnion Mounted Ball Valve for Reliable Flow Control
Reliavalve Trunnion Mounted Ball Valve: The Future of Flow ControlFlow control systems are essential to the safe and efficient operation of a wide range of industries, including oil and gas, chemical processing, and power generation. As such, the reliability and performance of flow control valves are crucial to the success of these industries. Recognizing this need, Reliavalve has designed and manufactured the Trunnion Mounted Ball Valve to deliver unmatched performance and reliability in these demanding environments.The Trunnion Mounted Ball Valve leverages cutting-edge engineering and advanced manufacturing techniques to offer end-users unparalleled flow control capabilities. One of the key features of this innovative valve is its bubble tight seal, which blocks the flow from upstream and downstream. This ensures that the valve is fully closed, preventing any unintended leakage or contamination that could negatively impact safety or production efficiency. Due to its high-performance capabilities, the Trunnion Mounted Ball Valve is designed to meet the strict standards set by API 6D and Gost.The Trunnion Mounted Ball Valve is also designed to be highly durable, able to withstand the challenging environments presented by a wide range of industries. This durability is achieved through the use of advanced materials and manufacturing techniques. The valve body is constructed from high-quality steel, which is highly resistant to corrosion, wear, and chemical damage. The ball and stem are also manufactured using the latest techniques to ensure that they can operate under high-pressure or high-temperature conditions without any problems.The Trunnion Mounted Ball Valve is also incredibly versatile, designed to be used in a diverse range of applications. Whether users need to control the flow of crude oil, natural gas, or corrosive chemicals, the valve delivers consistent and reliable performance. Its configuration can be customized to match the specific requirements of different industries, ensuring optimal flow control operations.Safety is another key feature of Reliavalve's Trunnion Mounted Ball Valve. Safety has been integrated into the design of the valve, and it has undergone rigorous testing to ensure that it can operate correctly under the most stringent conditions. Reliavalve has worked closely with various industries to develop procedures, guidelines, and training programs that ensure the safe operation of the valve, reducing the risks associated with flow control systems.In conclusion, Reliavalve's Trunnion Mounted Ball Valve is a game-changer that delivers the highest levels of performance, durability, versatility, and safety. This cutting-edge valve is a result of Reliavalve's constant commitment to innovation and engineering excellence. The company's mission is to provide reliable and innovative solutions that help industries optimize their operations, increase productivity, and improve safety. With the Trunnion Mounted Ball Valve, Reliavalve is revolutionizing the flow control industry, providing a solution that is set to shape the future of industries worldwide.
The Importance of Expansion Joints in Structures to Prevent Structural Collapse
Expansion joints are essential components of many structures, both large and small. These joints allow the materials of a structure to expand and contract safely as the temperature changes, ensuring the structural integrity of the building or bridge.In the case of bridges, expansion joints are particularly important. They help the bridge respond to changes in temperature and pressure caused by traffic, weather, and other environmental factors. Without expansion joints, bridges could suffer from structural damage, such as cracking or buckling, making them unsafe for travel.There are several types of expansion joints used in bridge construction. One of the most common types is the strip seal expansion joint. This type of joint is made up of multiple rubber or metal strips that are attached to the beams of the bridge. The strips allow the bridge to move slightly as the temperature changes, preventing unnecessary stress on the structure.Another type of expansion joint is the modular expansion joint. This type of joint is composed of several independent components that are bolted together. The components allow for movement in all directions, ensuring that the expansion and contraction of the bridge is evenly distributed.Finally, there is the sliding plate expansion joint. This type of joint consists of a series of metal plates that slide over one another as the bridge expands and contracts. The plates are typically held in place by bolts or other fasteners, allowing them to move independently while still providing support to the bridge.Regardless of the type of expansion joint used, it is important to ensure that it is properly installed and maintained. Regular inspections should be conducted to identify any signs of wear or damage, and repairs should be made as soon as possible to prevent further deterioration.In conclusion, expansion joints are critical components of many structures, particularly bridges. The use of the appropriate type of joint can help ensure the safety and structural integrity of these important structures. If you are involved in the construction or maintenance of a bridge, be sure to consult with a qualified engineer to determine the best type of expansion joint for your specific needs.
Top-Quality Rubber Hoses for Industrial Use in the UK
A Heavy Duty Rubber Hose for Industrial ApplicationsRubber hoses are undeniably one of the most crucial components of any industrial setting. They are responsible for transporting various fluids, gases, or even solids from one point to another with ease and accuracy. Different industrial settings require various hose types, but for heavy-duty applications, a rubber hose is undoubtedly the go-to option.A heavy-duty rubber hose is a type of industrial hose designed to withstand demanding working conditions such as high temperatures, high pressure, abrasion, and harsh chemicals. These hoses are typically made of synthetic rubber materials that offer superior durability and resistance to wear and tear.The Importance of Heavy-Duty Rubber HosesHeavy-duty rubber hoses are used in a wide range of applications, including construction, mining, agriculture, marine, and automotive industries. These hoses are designed to handle complex and challenging applications, where typical hoses may fail to perform. Some common benefits of heavy-duty rubber hoses include:1. Durability: Heavy-duty rubber hoses are designed to withstand harsh conditions and provide extended service life. They have a higher resilience to abrasion, puncture, and cuts, making them ideal for heavy-duty applications.2. High-temperature resistance: Rubber hoses can handle a wide range of temperatures without experiencing any deformation or damage. This quality makes them ideal for applications requiring high-temperature resistance.3. Chemical resistance: Heavy-duty rubber hoses are highly resistant to various chemicals that would otherwise damage typical hoses. This makes them suitable for the transportation of various fluids, including acids and alkalis.4. Application versatility: Heavy-duty rubber hoses can be used in different industrial settings, including hydraulic systems, pneumatic systems, and water delivery systems.Selecting the Right Heavy Duty Rubber HoseWhen choosing a heavy-duty rubber hose, it's essential to consider the specific application requirements. Here are a few factors to consider when selecting a heavy-duty rubber hose:1. Pressure rating: Make sure the hose can handle the required operating pressure of the application. It's crucial to select a hose with a higher operating pressure than your application requires to avoid any damage or failure.2. Temperature rating: Consider the temperature range of the application to ensure the hose can withstand these temperatures.3. Hose diameter: The diameter of the hose determines its flow rate. Select a hose with the appropriate diameter to achieve optimal flow rate and performance in your application.4. Abrasion resistance: For applications with high abrasion, choose hoses with higher abrasion-resistant covers. This ensures the hose's extended service life in a demanding environment.ConclusionA heavy-duty rubber hose is a crucial component in many industrial applications. These hoses offer superior durability, resistance to wear and tear, temperature, and chemical resistance, and versatility. It's essential to choose the right heavy-duty rubber hose that meets specific application requirements to ensure optimal performance, safety, and durability. Whether you need hoses to transport fluids, air, or gas in industrial applications, a durable, heavy-duty rubber hose is the best option to consider.
Versatile Metal Conveyor Belts for Diverse Applications
and Product Range.Metal Conveyor Belts: The Ultimate Solution for Every ApplicationConveyor belts are an essential component of industrial processes. They play a critical role in the transportation of materials, products, and goods across various stages of production and distribution. While there are different types of conveyor belts available in the market, metal conveyor belts are one of the most popular choices. They offer numerous advantages, such as strength, durability, and versatility, making them the ultimate solution for every application.At (need to remove brand name), we offer a wide range of metal conveyor belts that cater to various industries and applications. Our product range includes stainless steel belts, wire mesh belts, flat wire belts, chain belts, and modular belts, among others. Each of these belts features unique characteristics that make them suitable for specific purposes. Let's delve into each of them and see how they can benefit your business.Stainless Steel BeltsStainless steel belts are the most widely used metal belts in food, chemical, and pharmaceutical industries. They are highly resistant to corrosion, heat, and wear, making them ideal for conveying materials that require strict hygienic standards and harsh operating conditions. Stainless steel belts come in different grades, such as 304, 316, and 316L, to suit different environments and applications.Wire Mesh BeltsWire mesh belts consist of interlocked chains and metal wires that form a flat surface. They provide excellent airflow and drainage, making them perfect for applications such as drying, cooling, and heat treatment. Wire mesh belts are also highly durable, withstanding extreme temperatures and heavy loads.Flat Wire BeltsFlat wire belts are similar to wire mesh belts but consist of flat wires instead of interlocked chains. They offer smoother carrying surfaces, making them suitable for conveying delicate materials such as electronics and textiles. Flat wire belts also provide excellent heat and corrosion resistance, making them ideal for high-temperature and harsh environments.Chain BeltsChain belts are comprised of metal links that form a continuous loop. They are ideal for heavy-duty applications that require high strength and load-carrying capacity, such as mining, construction, and automotive industries. Chain belts can also withstand extreme temperatures, making them ideal for extreme heat or cold conditions.Modular BeltsModular belts are made of plastic or metal modules that interlock to form a continuous surface. They are ideal for applications that require precision, such as packaging, and can handle both light and heavy materials. Modular belts also come in different colors, making them suitable for color-coded sorting and identification.Overall, metal conveyor belts offer numerous benefits and are suitable for various applications. At (need to remove brand name), we provide a wide range of metal conveyor belts to cater to different industries and applications. Our belts are highly durable, reliable, and customizable to fit your exact needs. Contact us today to learn more about our products and how we can help improve your industrial processes.
Telescoping Flanged Fittings for Simplified Retrofitting Applications
Dismantling Joint for HDPE Pipe – The Solution for Retrofitting ApplicationsA flanged pipe system is an essential component of a fluid transfer system. However, in retrofitting applications, adding, repairing or replacing flanged fittings can be a challenging task. Traditional methods require cutting of the flange, removal of bolts, and breaking the joint to take out the damaged fittings. This approach involves high cost, labor, and downtime. To overcome this challenge, engineers have developed a solution in the form of Dismantling Joint for HDPE Pipe.A Dismantling Joint for HDPE Pipe is a special type of joint that allows the disassembly and reassembly of flanged pipe systems without cutting or breaking the pipe. It is suitable for retrofitting applications where the replacement of flanged fittings is necessary. The joint consists of two halves that can be separated without disrupting the pipeline's flow. The halves are held together by bolts, nuts, and a sealing gasket that ensures tightness and prevents leaks.The joint provides several advantages over traditional methods. With the Dismantling Joint, the installation and replacement of flanged fittings become more manageable, less time-consuming, and more cost-effective. Unlike traditional methods that require cutting of the flange, the joint eliminates the need for cutting and welding of the pipe, resulting in less downtime and disruption. Additionally, the joint's modular design allows for fast and easy assembly and disassembly, reducing labor costs.Another important advantage of the Dismantling Joint is its superior performance. The joint has a telescopic design that allows for flexibility in movement, expansion, and contraction of the pipeline. This feature makes it suitable for applications that involve temperature variations or ground movement. The joint's flexibility ensures that the system remains stable and permanent, preventing leaks and minimizing the risk of failure.The Dismantling Joint also provides versatility in its application. It can be used for various pipe materials, including HDPE, PVC, and cast iron, making it a go-to solution for retrofitting applications. The joint is also compatible with various flange standards, including ANSI, DIN, BS, and JIS, providing a solution for a wide range of piping systems.In conclusion, retrofitting applications involving flanged pipe systems require a solution that is easy to install, cost-effective, and reliable. The Dismantling Joint for HDPE Pipe provides the solution for adding, repairing, or replacing flanged fittings within a flanged pipe system. Its modular design, flexibility, and compatibility make it a versatile solution suitable for the majority of retrofitting applications.Therefore, if you are looking for a solution for your retrofitting application, consider the Dismantling Joint for HDPE Pipe. It reduces downtime, labor costs, and ensures long-term stability and reliability of your piping system. Remember, seamless fluid transfer depends on the quality of your piping system, and the Dismantling Joint for HDPE Pipe is one step closer towards achieving that goal.
Applications of Single Sphere Rubber Expansion Joints in Various Industries
Single Sphere Rubber Expansion Joint - Henan ShunyingHenan Shunying is a renowned manufacturer of industrial rubber products that offers a wide range of expansion joints, including single sphere rubber expansion joints. These types of expansion joints are typically used in various applications to prevent damage to the attached equipment, limit noise transmission, and reduce vibration caused by thermal expansion, pipeline misalignment, and ground settlement.Single sphere rubber expansion joints are designed to withstand large movements and pressure fluctuations. The single sphere feature helps it to absorb noise, decrease vibration, and compensate for slight misalignments. The joints are made of high-quality EPDM or NBR rubber, which is flexible, resilient and durable, and is resistant to water, heat, chemicals, and UV rays. This makes them ideal for a wide range of applications, especially in industrial and mechanical environments.The features of Single Sphere Rubber Expansion JointSingle sphere rubber expansion joints have several features that have made them popular in various industries such as chemical, petroleum, power generation, pharmaceuticals, mining, steel, water treatment, and HVAC.1. Flexibility:Flexibility is an essential feature of these expansion joints as it ensures that they can compensate for any axial, lateral or angular movements in the piping system. The flexible nature of the expansion joint helps reduce the risk of fatigue and cracking in pipelines and equipment.2. High-pressure resistance:Single sphere rubber joints are designed to withstand high-pressure applications, making them ideal for situations where pressure fluctuations occur regularly. They can withstand high bursts of pressure, thereby reducing the risk of equipment damage and potential leaks.3. Absorption of movements and vibrations:Single sphere rubber expansion joints are known for their ability to absorb movements and vibrations, reducing the risk of damage to connected equipment. Their ability to absorb vibrations also helps reduce noise transmission, which is essential in many industrial applications.4. Easy installation:Installation of single sphere rubber expansion joints is straightforward and requires minimal equipment. They are designed to fit perfectly into the pipeline, allowing for easy installation in limited spaces and hard-to-reach areas.5. Durability:Single sphere rubber expansion joints are durable and can withstand harsh working environments such as high temperatures, corrosive chemicals and UV radiation. They have a long lifespan and require minimal maintenance, making them cost-effective in the long run.Applications for Single Sphere Rubber Expansion JointSingle sphere rubber expansion joints are typically used in situations where pipeline misalignment, ground settlement or thermal expansion is expected, which includes the following applications:1. HVAC:Single sphere rubber expansion joints are commonly used in the HVAC industry, where they absorb thermal movements and vibrations caused by hot and cold air. Their flexibility also provides a seal between the air ducts and the equipment, reducing noise levels.2. Mining:Mining operations require flexible piping systems that can withstand harsh industrial environments. The single sphere rubber expansion joint is widely used in mining sites and can absorb excess vibrations and movements in the pipeline, reducing the risk of damage to equipment.3. Power generation:Single sphere rubber expansion joints are also used in power generation plants to reduce the risk of thermal expansion. They can also absorb vibrations from machinery, reducing noise, and prolonging the lifespan of connected equipment.4. Chemical plants:In chemical plants, the expansion joints can withstand corrosive chemicals as they are resistant to a wide range of chemicals, including acids, alkalis, and solvents, making them perfect for pipe connections.ConclusionSingle sphere rubber expansion joints are an essential component of an industrial piping system. They play an integral role in reducing the risk of damage to connected equipment, limiting noise transmission, and reducing vibration caused by thermal expansion, pipeline misalignment, and ground settlement. The Henan Shunying Single sphere rubber expansion joint is a quality product that offers flexibility, high-pressure resistance, easy installation, durability, and is suitable for various applications. In conclusion, the single sphere rubber expansion joint is a reliable solution that is both cost-effective and long-lasting.
Metal Insect Window and Door Fly Screen Wire Mesh - Types and Features
With the arrival of summer, the warmer weather brings about an influx of pesky flying insects, which can be a nuisance to homeowners. However, Smartex Screen Co., Ltd. has the perfect solution to this problem with their metal insect window and door fly screen wire mesh.The metal aluminum insect window and door fly screen wire mesh is one of the most popular products offered by Smartex Screen Co., Ltd. This fly screen mesh is made from premium quality metal aluminum, which is highly durable and long-lasting. The metal aluminum also provides added strength and durability to the fly screen, making it tear and weather-resistant. This is especially beneficial for homeowners as it ensures that the fly screen mesh remains effective even after prolonged exposure to harsh weather conditions.Smartex's metal insect screen is perfect for keeping pesky flying insects at bay, as it effectively blocks their entry into the house. The screen mesh is tightly woven, which ensures that even the smallest of insects cannot enter. This is especially beneficial for those who suffer from allergies as the screen mesh can prevent the entry of allergens into the house.Apart from being effective, the aluminum insect screen is also highly functional. It is easily installable on both windows and doors, and can be custom made to fit any window or door frame. The screen mesh is also transparent, which ensures that there is no obstruction to the view from the window.One of the best things about Smartex's metal insect window and door fly screen wire mesh is that it is low maintenance. It is easy to clean and does not require any special attention or care. This is especially beneficial for homeowners who lead busy lives and do not have the time or energy to spend on maintenance.Moreover, the metal aluminum insect window and door fly screen wire mesh is also an eco-friendly option. It does not involve any harmful chemicals or toxins, which makes it safe for both humans and the environment.Smartex Screen Co., Ltd. is a leading provider of insect screens, and their metal insect window and door fly screen wire mesh has been garnering rave reviews from customers across the world. They have always been committed to providing high-quality products and excellent customer service. Smartex's metal insect screen is perfect for homeowners who are looking for an effective, functional, and eco-friendly solution to keep flying insects at bay.In conclusion, Smartex Screen Co., Ltd. has revolutionized the way we deal with flying insects. Their metal insect window and door fly screen wire mesh is a game-changer, and is a must-have for every homeowner. It is effective, functional, low maintenance, and eco-friendly, which makes it the perfect solution for keeping pesky flying insects at bay.
Expert Tips for Conveyor Belt Splicing Techniques: Best Methods Revealed
Tips and Procedures for Splicing Conveyor Belts: Why Hot Vulcanization is RecommendedConveyor belts play a critical role in the transportation of varying products in different manufacturing and industrial settings. With the constant use of conveyor belts, it's inevitable that they will eventually wear and tear, break, and require repair. In such moments, conveyor belt splicing is essential.Several methods can be used to splice conveyor belts, including mechanical splicing and hot vulcanization. However, when it comes to choosing the best option, experts recommend hot vulcanization. This method involves the use of heat and pressure to bond the repair material to the damaged area, making it a durable, strong, and long-lasting solution.Why Choose Hot Vulcanization?Although hot vulcanization is more expensive and takes longer than mechanical splicing, it offers numerous benefits. Some of these benefits include:1. High Quality and Long-Lasting RepairsHot vulcanization enables you to achieve high-quality, long-lasting conveyor belt splicing solutions. The vulcanized splice is strong, durable, and often outlasts the original belt. The method ensures that you don't have to worry about conveyor downtime due to belt failure.2. Improved SafetyImproved safety is a significant benefit of vulcanized conveyor splicing. The process helps ensure that the conveyor belt is strong and direct to avoid accidents in the workplace. A damaged conveyor belt can result in injury or accidents that can cause significant damage to personnel, facilities, machinery, and products.3. Increased Conveyor EfficiencyVulcanized conveyor belt splicing helps optimize conveyor efficiency by minimizing downtime and reducing maintenance costs. This implies that you can focus more on production and less on conveyor maintenance, repair, and replacement.Procedures for Hot Vulcanization of Conveyor BeltsVulcanizing a conveyor belt involves several steps, including preparation, curing, and finishing. Here is a step-by-step guide to hot vulcanizing conveyor belts:1. Preparationa) Clean the damaged area by removing any dirt or debris.b) Mark the damaged section of the belt using a chalk or marker.c) Cut along the marked section using a repair strip cutter.d) Trim the end of the cut to make the repair strip neat.e) Buff both the belt and repair strip with a grinder to create a smooth surface.2. Curinga) Lay the belt ends together on a curing table and ensure that the splices are square.b) Apply hot vulcanizing material to both the belt ends.c) Use a putty knife to spread the material evenly.d) Position the repair strip and ensure that it covers the entire damaged area.e) Cover the repair strip with a release cloth.f) Use a vulcanizer to heat the splice to cure the hot vulcanizing material.3. Finishinga) Remove the release cloth.b) Cut any excess material from around the splice.c) By using a pry bar, carefully remove the splicing frame.d) Finally, inspect the conveyor belt to ensure the splice is cured correctly.In conclusion, conveyor belt splicing is a crucial process that should be taken seriously to ensure that the conveyor system operates smoothly and efficiently. Although there are several different belt splicing methods, hot vulcanization is the most reliable and durable solution. Following the proper hot vulcanization procedures will guarantee a high-quality repair that will last for an extended period.
Timers: A Comprehensive Guide Electric solenoid valve timers are essential components in the automation of fluid and gas control in various industries. These timers come in different designs and functionalities to suit various applications and requirements. In this blog, we will guide you through an in-depth understanding of solenoid valve timers and their applications. What are Solenoid Valve Timers? A solenoid valve timer is an electrical device that controls the opening and closing of solenoid valves according to pre-set time intervals. The timer regulates the process flow by providing an electrical signal that triggers the solenoid valve to open, close, or partially open at precise times. They are also used to prevent system overflows, limit liquid levels, and to sequence the operation of pumps and compressors. How Do Solenoid Valve Timers Work? Solenoid valve timers operate by using an electronic timer circuit and a solenoid valve that controls the flow of fluid or gas through the valve body. The timer is pre-set to control the duration of the valve's open state. The timer circuit sends a signal to the solenoid valve, causing it to open or close. The solenoid valve is an electromechanical device that converts electrical energy into mechanical action. Applications of Solenoid Valve Timers Solenoid valve timers are used in many industries and applications, such as: 1. Irrigation Systems Solenoid valve timers are used in irrigation systems to automate the watering process. The timer controls the water flow through the solenoid valve, ensuring that plants or crops receive consistent and regulated amounts of water. 2. Industrial Automation Solenoid valve timers are used in industrial automation systems to control the flow of fluids and gases through different processes. They are also used in storage tanks, boilers, and pumps to regulate their operation. 3. HVAC Systems Heating, Ventilation, and Air Conditioning (HVAC) systems utilize solenoid valve timers to control the flow of refrigerants, coolants, and airflow. The timer regulates the timing of the cycles of the components to ensure that the system operates efficiently. 4. Medical Equipment Solenoid valve timers are used in medical equipment and laboratory applications to control the flow of fluids and gases accurately. They are commonly used in hospital laundry systems and automated laboratory equipment. Factors to Consider When Choosing a Solenoid Valve Timer When selecting a solenoid valve timer, you must consider the following factors: 1. Timer Type Solenoid valve timers come in different types, including on-delay, off-delay, pulse, and interval timer types. Each type has its unique function and duration, depending on the application requirements. 2. Timing Range The timing range is the number of seconds, minutes, or hours that the solenoid valve remains open or closed. Consider the timing range of the timer according to the application. 3. Power Requirements The timer power requirements should match those of the solenoid valve or the equipment the timer is controlling. Select a timer that operates on the required voltage and frequency. 4. Interface and Mounting Ensure that the timer has an interface and mounting design that suits the device or system it will control. Conclusion Solenoid valve timers are essential in the automation of fluid and gas control processes in various industries. Understanding their functions and applications is crucial in selecting the right type of timer for your system. Remember to consider the timing range, power requirements, interface, and mounting design when selecting a solenoid valve timer for your application. In summary, electric solenoid valve timers are critical in the control and regulation of fluid and gas flow in many applications. Tameson offers a wide range of solenoid valve timers suitable for various industries. Browse our website or contact us for more information.