China's Growing Conveyor Belt Market: Insights, Analysis and Forecast 2016-2020
By:Admin
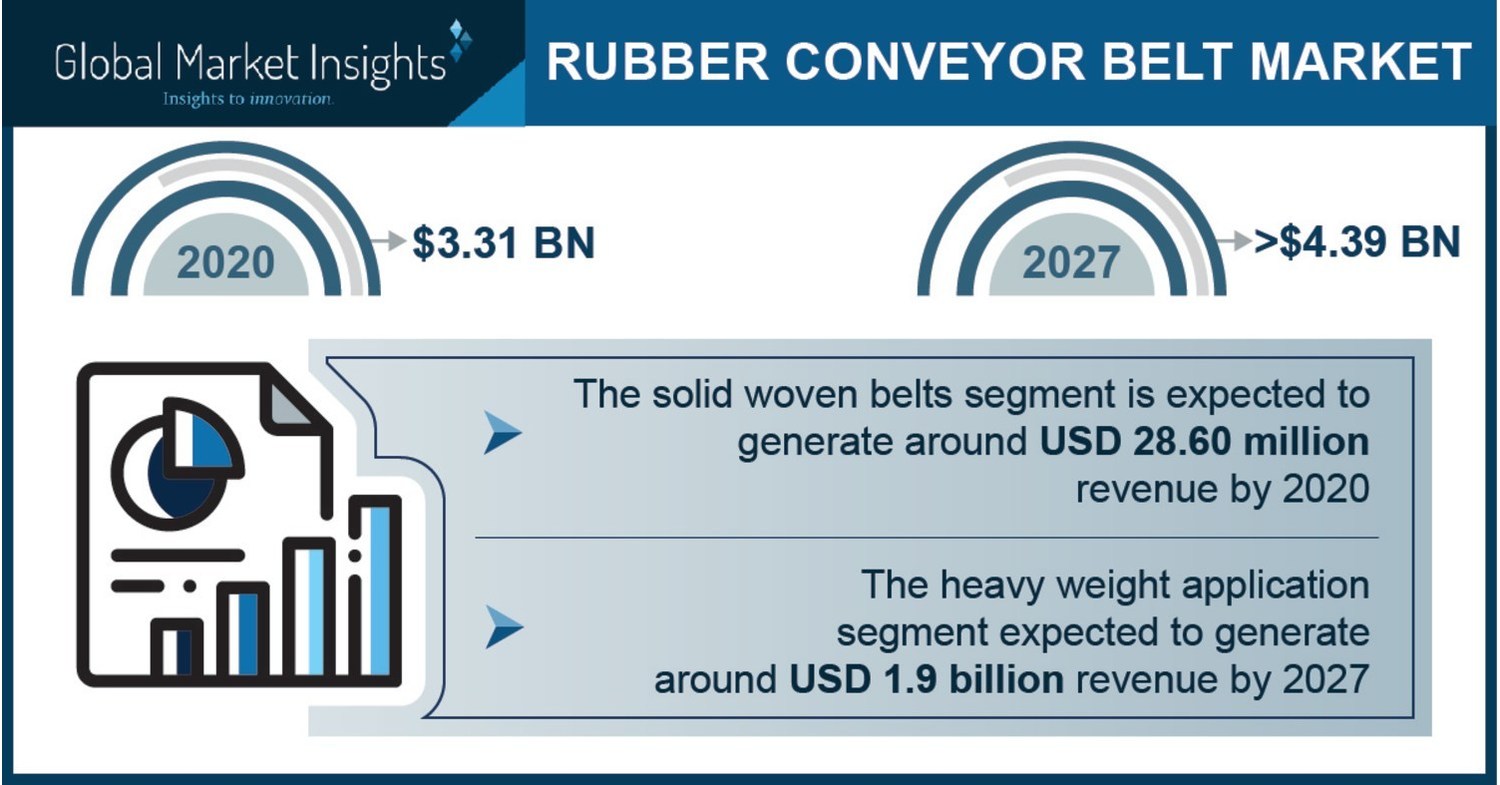
The conveyor belt market in China is expected to grow at a CAGR of over 5% during the period 2016-2020. This growth can be attributed to the increasing demand for automated machinery and the need for efficient material handling systems across various industries.
The expanding industrial sector in China is driving the demand for conveyor belts. The growing automotive and logistics industries have also contributed to the growth of the conveyor belt market. In addition, the increasing adoption of e-commerce and online shopping has led to a surge in demand for conveyor belts in the warehousing and distribution sector.
Furthermore, the Chinese government's initiatives to promote infrastructure development are anticipated to boost the demand for conveyor belts in the construction and mining industries. The "One Belt, One Road" initiative, which aims to strengthen economic and trade ties between China and other countries, is expected to drive the growth of the conveyor belt market in the region.
In terms of product type, the rubber conveyor belt segment accounts for a significant share of the market, owing to its durability, flexibility, and cost-effectiveness. The steel cord conveyor belt segment is also expected to witness significant growth due to its high strength and resistance to impact and abrasion.
Geographically, the eastern region of China is the dominant market for conveyor belts, thanks to the presence of major industrial hubs in cities such as Shanghai and Guangzhou. However, the western region is also expected to witness significant growth, backed by the government's focus on developing this region.
Several companies operate in the conveyor belt market in China, including {the Conveyor Belt}, which is a leading player in the industry. It offers a wide range of conveyor belts for various applications, such as mining, steelworks, ports, and power plants.
However, the market is highly fragmented, with the presence of several small and medium-sized players. The intense competition has compelled companies to focus on product innovation and development, along with cost management to maintain their market position.
In conclusion, the conveyor belt market in China is poised for significant growth in the coming years, backed by the expanding industrial sector and the government's infrastructure development initiatives. The increasing adoption of e-commerce and online shopping is also expected to drive demand for conveyor belts in the warehousing and distribution sector. Companies operating in the market need to focus on product innovation, development, and cost management to maintain their market position in this highly fragmented industry.
Company News & Blog
Discover the Benefits of Expansion Joint Rubber Gaskets for Optimal Performance
Rubber gaskets are an essential component in various industrial applications that require sealing between two surfaces to prevent any leakage. One of the most significant challenges faced by industries is the expansion and contraction of pipes due to extreme temperatures. The solution to this problem is the use of expansion joint rubber gaskets, which allows for movement and flexibility while maintaining a tight seal.One of the leading manufacturers of expansion joint rubber gaskets is a company that has been in the industry for over two decades. They specialize in providing high-quality industrial rubber products to their clients across various sectors, including oil and gas, water treatment, and food processing.Their expansion joint rubber gaskets are made of high-grade materials, which offer maximum durability, flexibility, and resistance to extreme temperatures and pressure. The gaskets are designed to allow for axial, lateral, and angular movement, making them ideal for use in piping systems that undergo frequent expansion and contraction.What makes their expansion joint rubber gaskets unique is their ability to withstand harsh environmental conditions. The gaskets can resist corrosion and chemical attacks, making them suitable for use in aggressive environments where conventional gaskets may fail to offer adequate protection.The company's expansion joint rubber gaskets are available in various widths, lengths, and thicknesses to provide an exact fit for different applications. They offer customized solutions to their clients, ensuring that the gaskets meet their specific requirements.The company's commitment to ensuring customer satisfaction is demonstrated by their stringent quality control measures. They have a team of experienced technicians who conduct rigorous tests on all their products before they leave the factory to ensure that they meet the required standards.In addition to their expansion joint rubber gaskets, the company also offers a wide range of industrial rubber products such as seals, gaskets, hoses, and O-rings. Their products are widely used in different industries due to their reliability, durability, and performance.The company's success is rooted in their dedication to providing top-quality products and exceptional customer service. They have a team of experts who provide technical support to their clients, ensuring that they have the right product for their specific needs.Their expansion joint rubber gaskets have been widely recognized for their performance and quality by different industry bodies. They have received several certifications, including the ISO 9001:2015 quality management system certification, which demonstrates their commitment to providing high-quality products.In conclusion, the use of expansion joint rubber gaskets is crucial in various industrial applications that require sealing between two surfaces. The company has established itself as a leading manufacturer of high-quality rubber products, including expansion joint rubber gaskets. Their products are reliable, durable, and offer maximum protection in harsh environmental conditions. With their commitment to quality and customer satisfaction, the company is well-positioned to continue providing innovative solutions to their clients across different sectors.
Expert Tips for Conveyor Belt Splicing Techniques: Best Methods Revealed
Tips and Procedures for Splicing Conveyor Belts: Why Hot Vulcanization is RecommendedConveyor belts play a critical role in the transportation of varying products in different manufacturing and industrial settings. With the constant use of conveyor belts, it's inevitable that they will eventually wear and tear, break, and require repair. In such moments, conveyor belt splicing is essential.Several methods can be used to splice conveyor belts, including mechanical splicing and hot vulcanization. However, when it comes to choosing the best option, experts recommend hot vulcanization. This method involves the use of heat and pressure to bond the repair material to the damaged area, making it a durable, strong, and long-lasting solution.Why Choose Hot Vulcanization?Although hot vulcanization is more expensive and takes longer than mechanical splicing, it offers numerous benefits. Some of these benefits include:1. High Quality and Long-Lasting RepairsHot vulcanization enables you to achieve high-quality, long-lasting conveyor belt splicing solutions. The vulcanized splice is strong, durable, and often outlasts the original belt. The method ensures that you don't have to worry about conveyor downtime due to belt failure.2. Improved SafetyImproved safety is a significant benefit of vulcanized conveyor splicing. The process helps ensure that the conveyor belt is strong and direct to avoid accidents in the workplace. A damaged conveyor belt can result in injury or accidents that can cause significant damage to personnel, facilities, machinery, and products.3. Increased Conveyor EfficiencyVulcanized conveyor belt splicing helps optimize conveyor efficiency by minimizing downtime and reducing maintenance costs. This implies that you can focus more on production and less on conveyor maintenance, repair, and replacement.Procedures for Hot Vulcanization of Conveyor BeltsVulcanizing a conveyor belt involves several steps, including preparation, curing, and finishing. Here is a step-by-step guide to hot vulcanizing conveyor belts:1. Preparationa) Clean the damaged area by removing any dirt or debris.b) Mark the damaged section of the belt using a chalk or marker.c) Cut along the marked section using a repair strip cutter.d) Trim the end of the cut to make the repair strip neat.e) Buff both the belt and repair strip with a grinder to create a smooth surface.2. Curinga) Lay the belt ends together on a curing table and ensure that the splices are square.b) Apply hot vulcanizing material to both the belt ends.c) Use a putty knife to spread the material evenly.d) Position the repair strip and ensure that it covers the entire damaged area.e) Cover the repair strip with a release cloth.f) Use a vulcanizer to heat the splice to cure the hot vulcanizing material.3. Finishinga) Remove the release cloth.b) Cut any excess material from around the splice.c) By using a pry bar, carefully remove the splicing frame.d) Finally, inspect the conveyor belt to ensure the splice is cured correctly.In conclusion, conveyor belt splicing is a crucial process that should be taken seriously to ensure that the conveyor system operates smoothly and efficiently. Although there are several different belt splicing methods, hot vulcanization is the most reliable and durable solution. Following the proper hot vulcanization procedures will guarantee a high-quality repair that will last for an extended period.
Durable Slurry Hoses for Handling Abrasive Materials
Slurry hose and mud hose are crucial components in the operations of mines and quarries. They play a vital role in transporting abrasive and viscous slurries, which are byproducts of mining and quarrying activities. Without these hoses, the transportation of these materials would be challenging and costly.Recognizing the importance of slurry hoses and mud hoses, China's rubber industry has been actively manufacturing and supplying these vital components to various industries across the globe. China is a recognized hub for rubber production, and its manufacturers are renowned for their exceptional engineering expertise, high-quality materials, and user-friendly designs.One such manufacturer is [insert brand name], a leading supplier and manufacturer of slurry hoses and mud hoses. The company has been manufacturing and supplying these hoses for over a decade, providing exceptional service to its clients across the globe. By integrating the latest technology and consistently improving their manufacturing processes, they have been able to produce superior quality hoses at competitive prices.Slurry hoses are primarily designed to handle abrasive and viscous slurries. The hoses are made of high-quality blended rubber, which can withstand the abrasive nature of the materials, reducing the risk of wear and tear. The external bolt-on flanges design of the hoses allows for easy installation, uninterrupted free flow and makes maintenance much easier.Mud hoses, on the other hand, are designed to handle heavy mud and sludge materials. The hoses are made of premium quality materials that can withstand the heavy pressure of the materials transported. The smooth interior of the hose facilitates the smooth flow of materials, preventing blockages and ensuring a consistent flow.[Insert brand name] has gone beyond producing standard slurry hoses and mud hoses. The manufacturer also produces customized hoses to meet the specific needs of clients. Their team of experts utilizes the latest engineering software to design and produce hoses that are specific to individual requirements. Whether it is with regards to shape, length, or diameter, [insert brand name] always delivers quality hoses that meet the demands of the client.Quality is essential to the team at [insert brand name]. The company's professional team of engineers and technicians ensures that the manufacturing process follows strict guidelines and is compliant with international standards such as ISO and API. They use high-quality raw materials to ensure that the end product is durable, reliable, and safe.In addition to the superior quality of their products, [insert brand name] also prides itself on its exceptional customer service. The team is dedicated to providing excellent service to clients, ensuring that all their requirements are met promptly and efficiently. They have an excellent after-sales service, which ensures that clients receive the necessary support and assistance they require throughout the life of the product.The company also offers competitive pricing for their products without compromising on the quality. Their pricing strategy is aimed at providing affordable solutions to their clients without sacrificing the quality of their products. This strategy has played a considerable role in making [insert brand name] a preferred choice for clients across the globe.In conclusion, slurry hose and mud hose are essential components of the mining and quarrying industry. The quality of the hoses used can affect the productivity, cost, and safety of the operations. Investing in high-quality hoses from a reputable supplier such as [insert brand name] is crucial for any mining or quarrying operation. With their exceptional products, competitive pricing, and excellent customer service, [insert brand name] is a manufacturing industry leader that has become a trusted partner to clients worldwide.
Understanding the Definition and Importance of Expansion Joints in Various Applications
Title: Understanding Steam Expansion Joints: An Essential GuideIntroduction:In any industrial setting where steam pipes are essential, the proper functioning of expansion joints becomes crucial. Expansion joints play a vital role in compensating for the expansion and contraction resulting from temperature changes. In this blog, we will delve into the definition, significance, and working principle of steam expansion joints, shedding light on their importance in various industries. Join us as we demystify the world of steam expansion joints!Chapter 1: The Basics of Expansion JointsTo understand steam expansion joints, it is essential to grasp the concept of expansion joints themselves. Expansion joints are couplings designed to enable movement in a particular direction, allowing for compensatory adjustments due to thermal expansion and contraction. These movements are caused by temperature fluctuations, which can have adverse effects if not addressed effectively.Chapter 2: The Significance of Steam Expansion Joints2.1 Ensuring System Integrity:In steam-based systems, temperature changes can result in expansion or contraction of the pipeline. Steam expansion joints are specifically designed to accommodate these shifts while ensuring system integrity. By reducing stress on interconnected components, expansion joints help prevent pipe ruptures, leaks, and other potential hazards caused by thermal strain.2.2 Enhancing Safety and Reliability:The installation of steam expansion joints is crucial for compliance with industry safety standards and regulations. By maintaining proper alignment and allowing for required movement, expansion joints safeguard the entire system from undue stress, preventing catastrophic failures and accidents.Chapter 3: Working Principle of Steam Expansion Joints3.1 Absorbing Thermal Expansion:Steam expansion joints are designed to absorb the linear expansion or contraction that occurs within pipes due to temperature changes. These joints typically consist of bellows, which are flexible, convoluted components that can expand or contract, compensating for the thermal displacement. This elasticity ensures the smooth operation of the entire system.3.2 Types of Steam Expansion Joints:There are several types of steam expansion joints, including axial, universal, gimbal, hinged, and pressure-balanced joints, each with its unique characteristics. Understanding the specific requirements of your steam system is essential for choosing the most suitable expansion joint design.Chapter 4: Applications of Steam Expansion Joints4.1 Power Generation:In power plants, steam expansion joints play a critical role in various applications, such as turbine bypass, flue gas desulfurization systems, and steam piping. By accommodating thermal expansions in these high-temperature environments, expansion joints ensure uninterrupted power generation and prevent costly breakdowns.4.2 Oil and Gas Industries:Steam expansion joints find widespread use in the oil and gas industries. These joints enable efficient operation of steam injection systems and various pipeline connections, mitigating the impact of temperature fluctuations inherent in steam-based processes.4.3 Manufacturing and Processing:Many manufacturing facilities rely on steam for their operations. From steam-heated treatment processes to heat exchangers, steam expansion joints are crucial in maintaining efficient production by absorbing thermal stresses and preventing damage to vital equipment.Chapter 5: Steam Expansion Joint Maintenance and InspectionTo ensure the seamless functioning and longevity of steam expansion joints, regular maintenance and inspection are vital. Adequate assessment of bellows fatigue, leakage, corrosion, and alignment issues will help identify potential problems before they escalate, allowing for timely repairs or replacements.Conclusion:Steam expansion joints provide a cost-effective and reliable solution to compensate for thermal expansion and contraction in various industries. By understanding their fundamental principles, significance, and proper maintenance, businesses can ensure the continued safety and efficiency of their steam systems. Take the necessary steps to protect your assets and optimize the performance of your steam-based processes by prioritizing steam expansion joint installations and maintenance.
Find out how to fix a leaking main valve with the help of the side knob
, Leaking Valve, Main Valve, Knob, Water Flow, Water Pressure, Plumbing Repairs.Have you ever experienced a leaking main valve at home? It can be frustrating and concerning, especially if you don't know how to fix it. Main valves are important because they control the water flow and pressure in your home's plumbing system. When they start leaking, it's important to take action to prevent further damage.One question you may have is what the knob on the side of the valve does and if it can stop the leak. The knob is called the packing nut, and it is used to control the packing material inside the valve. The packing material is placed around the valve stem, which is the part that moves up and down to control the water flow. The packing material prevents water from leaking around the valve stem.If your main valve is leaking, it's possible that the packing material has worn out or become loose, allowing water to escape. Turning the packing nut can sometimes tighten the packing material and stop the leak. However, this is only a temporary fix, and you may need to replace the packing material or the entire valve to fully resolve the issue.When dealing with a leaking main valve, it's important to take safety precautions. Turn off the water supply to your house before attempting to make any repairs. This will prevent any accidents or further damage to your plumbing system. If you are not comfortable making the repairs yourself, it's best to call a professional plumber to fix the issue.In addition to safety precautions, it's important to understand the basics of plumbing repairs. A leaking main valve is just one example of a common plumbing issue that homeowners may face. Knowing how to identify the problem and its possible solutions can save you time, money, and stress in the long run.When it comes to plumbing repairs, prevention is the best solution. Regular maintenance and inspections can help you identify and address any issues before they become major problems. This includes checking for leaks, inspecting pipes and valves, and monitoring water pressure and flow.In conclusion, if you are experiencing a leaking main valve, don't panic. The knob on the side, or the packing nut, can sometimes stop the leak temporarily, but you should still have a professional plumber inspect and repair the issue. Remember to take safety precautions and keep up with regular plumbing maintenance to prevent future issues. With these tips, you can keep your plumbing system running smoothly and avoid any major problems down the road.
Telescoping Flanged Fittings for Simplified Retrofitting Applications
Dismantling Joint for HDPE Pipe – The Solution for Retrofitting ApplicationsA flanged pipe system is an essential component of a fluid transfer system. However, in retrofitting applications, adding, repairing or replacing flanged fittings can be a challenging task. Traditional methods require cutting of the flange, removal of bolts, and breaking the joint to take out the damaged fittings. This approach involves high cost, labor, and downtime. To overcome this challenge, engineers have developed a solution in the form of Dismantling Joint for HDPE Pipe.A Dismantling Joint for HDPE Pipe is a special type of joint that allows the disassembly and reassembly of flanged pipe systems without cutting or breaking the pipe. It is suitable for retrofitting applications where the replacement of flanged fittings is necessary. The joint consists of two halves that can be separated without disrupting the pipeline's flow. The halves are held together by bolts, nuts, and a sealing gasket that ensures tightness and prevents leaks.The joint provides several advantages over traditional methods. With the Dismantling Joint, the installation and replacement of flanged fittings become more manageable, less time-consuming, and more cost-effective. Unlike traditional methods that require cutting of the flange, the joint eliminates the need for cutting and welding of the pipe, resulting in less downtime and disruption. Additionally, the joint's modular design allows for fast and easy assembly and disassembly, reducing labor costs.Another important advantage of the Dismantling Joint is its superior performance. The joint has a telescopic design that allows for flexibility in movement, expansion, and contraction of the pipeline. This feature makes it suitable for applications that involve temperature variations or ground movement. The joint's flexibility ensures that the system remains stable and permanent, preventing leaks and minimizing the risk of failure.The Dismantling Joint also provides versatility in its application. It can be used for various pipe materials, including HDPE, PVC, and cast iron, making it a go-to solution for retrofitting applications. The joint is also compatible with various flange standards, including ANSI, DIN, BS, and JIS, providing a solution for a wide range of piping systems.In conclusion, retrofitting applications involving flanged pipe systems require a solution that is easy to install, cost-effective, and reliable. The Dismantling Joint for HDPE Pipe provides the solution for adding, repairing, or replacing flanged fittings within a flanged pipe system. Its modular design, flexibility, and compatibility make it a versatile solution suitable for the majority of retrofitting applications.Therefore, if you are looking for a solution for your retrofitting application, consider the Dismantling Joint for HDPE Pipe. It reduces downtime, labor costs, and ensures long-term stability and reliability of your piping system. Remember, seamless fluid transfer depends on the quality of your piping system, and the Dismantling Joint for HDPE Pipe is one step closer towards achieving that goal.
Timers: A Comprehensive Guide Electric solenoid valve timers are essential components in the automation of fluid and gas control in various industries. These timers come in different designs and functionalities to suit various applications and requirements. In this blog, we will guide you through an in-depth understanding of solenoid valve timers and their applications. What are Solenoid Valve Timers? A solenoid valve timer is an electrical device that controls the opening and closing of solenoid valves according to pre-set time intervals. The timer regulates the process flow by providing an electrical signal that triggers the solenoid valve to open, close, or partially open at precise times. They are also used to prevent system overflows, limit liquid levels, and to sequence the operation of pumps and compressors. How Do Solenoid Valve Timers Work? Solenoid valve timers operate by using an electronic timer circuit and a solenoid valve that controls the flow of fluid or gas through the valve body. The timer is pre-set to control the duration of the valve's open state. The timer circuit sends a signal to the solenoid valve, causing it to open or close. The solenoid valve is an electromechanical device that converts electrical energy into mechanical action. Applications of Solenoid Valve Timers Solenoid valve timers are used in many industries and applications, such as: 1. Irrigation Systems Solenoid valve timers are used in irrigation systems to automate the watering process. The timer controls the water flow through the solenoid valve, ensuring that plants or crops receive consistent and regulated amounts of water. 2. Industrial Automation Solenoid valve timers are used in industrial automation systems to control the flow of fluids and gases through different processes. They are also used in storage tanks, boilers, and pumps to regulate their operation. 3. HVAC Systems Heating, Ventilation, and Air Conditioning (HVAC) systems utilize solenoid valve timers to control the flow of refrigerants, coolants, and airflow. The timer regulates the timing of the cycles of the components to ensure that the system operates efficiently. 4. Medical Equipment Solenoid valve timers are used in medical equipment and laboratory applications to control the flow of fluids and gases accurately. They are commonly used in hospital laundry systems and automated laboratory equipment. Factors to Consider When Choosing a Solenoid Valve Timer When selecting a solenoid valve timer, you must consider the following factors: 1. Timer Type Solenoid valve timers come in different types, including on-delay, off-delay, pulse, and interval timer types. Each type has its unique function and duration, depending on the application requirements. 2. Timing Range The timing range is the number of seconds, minutes, or hours that the solenoid valve remains open or closed. Consider the timing range of the timer according to the application. 3. Power Requirements The timer power requirements should match those of the solenoid valve or the equipment the timer is controlling. Select a timer that operates on the required voltage and frequency. 4. Interface and Mounting Ensure that the timer has an interface and mounting design that suits the device or system it will control. Conclusion Solenoid valve timers are essential in the automation of fluid and gas control processes in various industries. Understanding their functions and applications is crucial in selecting the right type of timer for your system. Remember to consider the timing range, power requirements, interface, and mounting design when selecting a solenoid valve timer for your application. In summary, electric solenoid valve timers are critical in the control and regulation of fluid and gas flow in many applications. Tameson offers a wide range of solenoid valve timers suitable for various industries. Browse our website or contact us for more information.
New Innovation: Advanced Technology for Flotation Machines - Stator and Rotor Improvements
Title: Groundbreaking Flotation Stator and Rotor Technology Revolutionizes Industry EfficiencyIntroduction:As industries across the globe continue to push boundaries and strive for increased efficiency and sustainability, one company at the forefront of innovation has developed a game-changing technology. (Company Name), a renowned leader in engineering solutions, has announced the successful development of an advanced Flotation Stator and Rotor system that promises to revolutionize various industrial processes. By combining cutting-edge design with years of industry expertise, (Company Name) is set to transform the way industries tackle flotation separation, enhancing productivity, and reducing environmental impact.Body:1. Driving Industry Efficiency:The Flotation Stator and Rotor technology developed by (Company Name) is set to optimize the efficiency of various industrial processes. Flotation separation, a key process in industries such as mining, wastewater treatment, and oil extraction, involves separating different components based on their hydrophobicity. The Flotation Stator and Rotor system improves this process by providing a stable and efficient environment for particle-surface interactions, resulting in enhanced separation efficiency. This breakthrough technology is expected to significantly reduce energy consumption and operational costs, while increasing overall productivity.2. Enhanced Design and Performance:The newly developed Flotation Stator and Rotor system features an innovative design that prioritizes durability and performance. Utilizing state-of-the-art materials and advanced engineering techniques, (Company Name) has created a system capable of withstanding harsh operating conditions, such as high temperatures and corrosive environments. The stator and rotor components boast improved wear resistance, delivering extended service life and reducing the need for frequent maintenance. This not only enhances operational reliability but also reduces downtime, ensuring uninterrupted production cycles.3. Sustainable Solutions:In today's world, sustainability underpins the success of any technological advancement. (Company Name) understands the importance of eco-friendly solutions and has incorporated this ethos into the design of the Flotation Stator and Rotor system. The technology minimizes the environmental impact by reducing the usage of chemicals and reagents required for the flotation process. Additionally, its improved separation efficiency allows for better resource utilization, ensuring minimal waste generation. This commitment to sustainability aligns with ever-increasing global environmental regulations and positions (Company Name) as a responsible industry leader.4. Diverse Industrial Applications:The versatility of the Flotation Stator and Rotor technology enables its application across various industries. In the mining sector, where efficient ore extraction is paramount, the technology can enhance mineral recovery rates and reduce the consumption of chemicals used in the flotation process. In wastewater treatment, this innovation assists in the removal of contaminants, improving the quality of treated water discharge. Furthermore, the oil and gas industry can benefit from increased separation efficiency, accelerating the extraction process while minimizing environmental impact.5. Advancing Industry Standards:By introducing this groundbreaking Flotation Stator and Rotor technology, (Company Name) is spearheading a new era of industrial efficiency. The innovative design and sustainable features of the system have set new standards, paving the way for a more sustainable and productive future. As other market players take note of this transformative technology, it is likely to lead to further advancements in the sector, triggering a positive ripple effect across industries worldwide.Conclusion:With its advanced Flotation Stator and Rotor system, (Company Name) has positioned itself as a trailblazer in the quest for increased industrial efficiency and sustainability. This game-changing technology promises to transform flotation separation processes across diverse industries, ensuring enhanced productivity, reduced operational costs, and decreased environmental impact. As industries embrace these innovative solutions, the world moves closer to achieving a more sustainable and prosperous future.